problem
solving
課題解決
弊社が今までに提供してきた改善事例を紹介いたします。
CACE01 アルミ押出部品 切削加工からプレス加工へ加工方法変更
当初
アルミ押出品の加工。穴明及び45°カットをマシニングにて切削加工で行っていた。
改善
穴明及び45°カットを金型プレス加工にすることにより、生産数量が大幅UP。
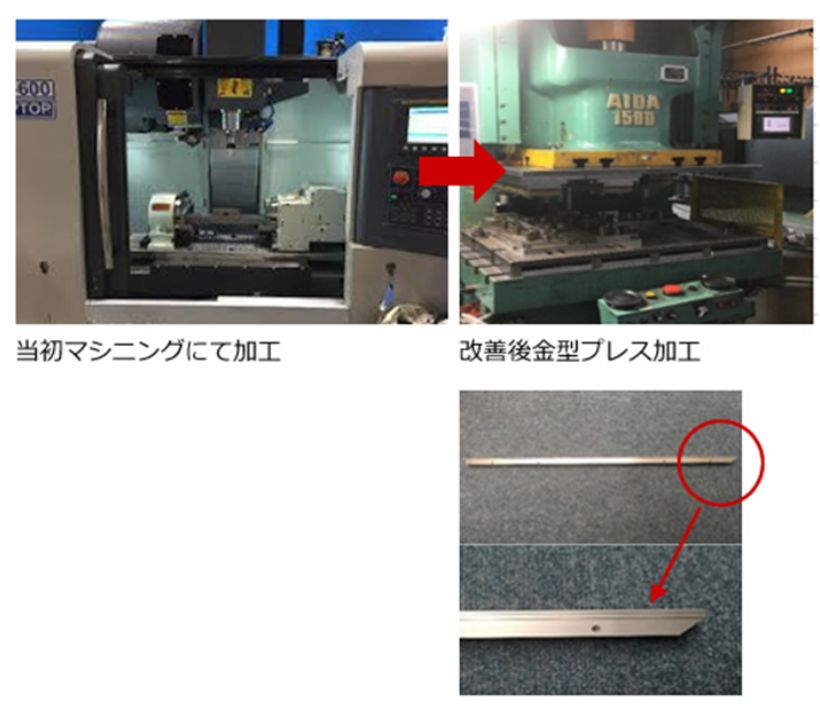
CACE02 ステンレス製筐体 溶接構造から曲げ絞り構造へ変更
当初
角度の違う排水部を別パーツで製作し、それを本体にTIG溶接していた。
改善
別パーツを廃止し本体と一体化形状を提案。絞りを斜め構造として排水性クリア。
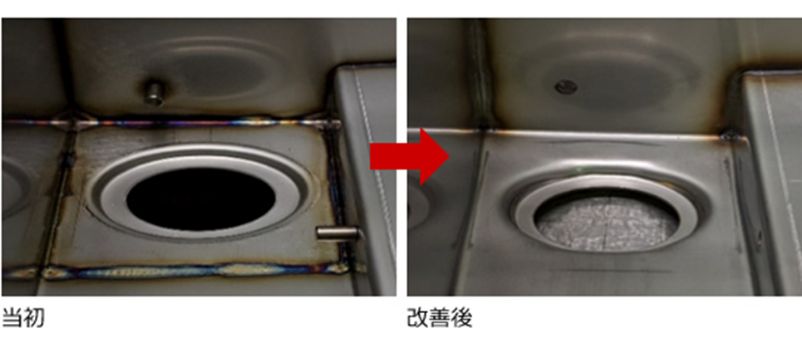